So That Society and Moritsune
Will Remain Sustainable
for the Next 1000 Years.
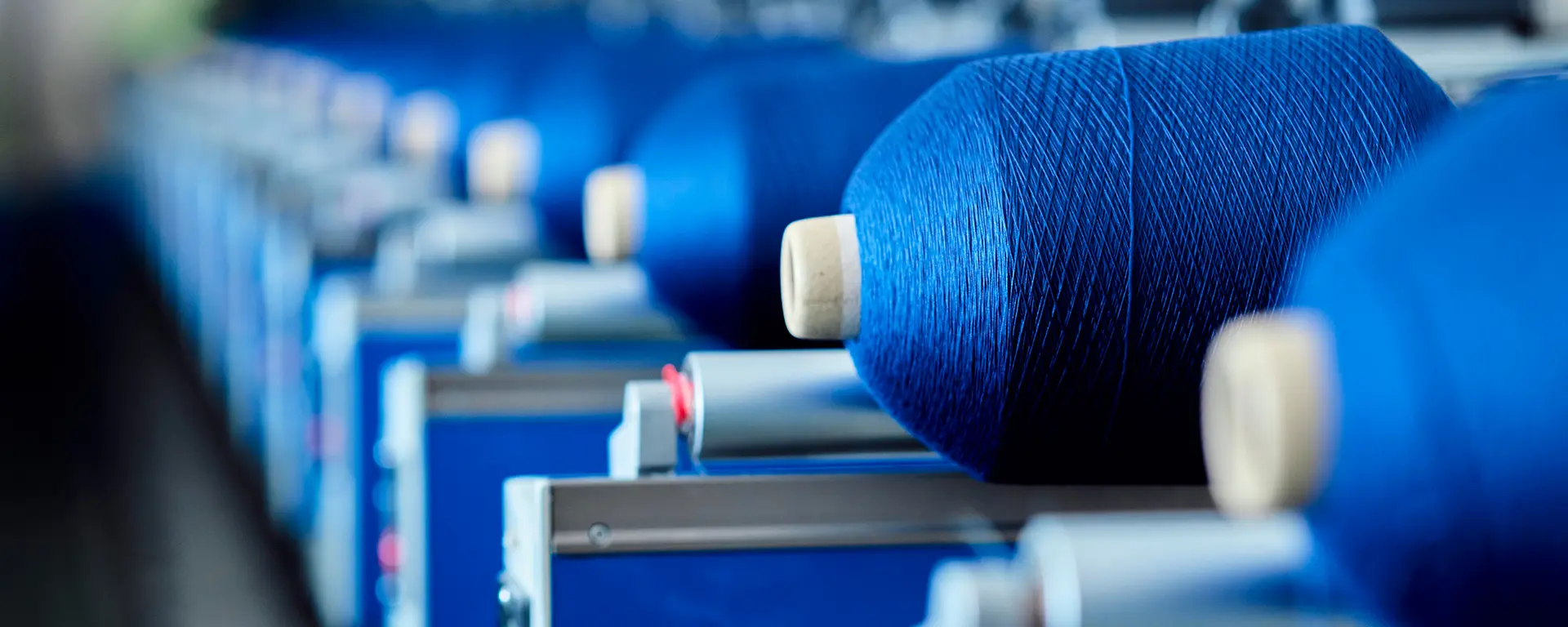
Sustainable Development Goals
So That Society and Moritsune
Will Remain Sustainable
for the Next 1000 Years.
We have made the "SDGs Declaration" to strengthen our efforts towards achieving the SDGs (Sustainable Development Goals).
By sharing a common understanding of issues across the organization and working on specific activities to resolve them, we will put into practice activities aimed at realizing a sustainable society.
We are actively recruiting women, as we believe this will lead to stable employment for the company. We are also reviewing and improving all of our internal systems to make the most of women's abilities.
For example, we are creating a remote work system that utilizes ICT, and a new organizational structure that covers muscle and physical strength. We would like to continue creating opportunities for women to expand their fields of activity.
*As of November 2024
Our goal is to promote "decent work," a non-discriminatory way of working, and to achieve essential prosperity while continuing economic growth.
The Earth's resources are not infinite. We use responsible and sustainable production methods that aim to utilize resources efficiently, coexist with nature, and recycle resources. We also work on product development that allows for sustainable consumption and production.
The Global Recycle Standard (GRS) is an international voluntary standard that covers the social and environmental aspects, quality, and legal compliance of the processing and manufacturing of recycled products. We are currently in the process of obtaining certification.
Certification requires that more than 50% of raw materials are recycled, that chemicals containing hazardous substances are regulated, etc. In addition, company-level energy usage data and reduction plans are submitted, and employee labor and wage systems, the presence or absence of discrimination, and internal controls of companies and unions are also examined.
Compared to other fuels, LPG (liquefied petroleum gas) emits less carbon dioxide (CO2), nitrogen oxides (NOx), and particulate matter (PM) when burned. Using LPG contributes to reducing environmental problems such as air pollution and global warming.
100% polyester and 100% nylon materials can be recycled if the correct processes are followed, and we are beginning efforts to promote this.
We purchased a bleaching machine in collaboration with Sanyo Trading Co., Ltd., and are now bleaching used fibers and handing them over to our partner companies. We also purchase yarn that has been processed by our partner companies and process it to create new products.
The ocean is essential to human life and livelihood, and to our company, which uses the Earth's resources. We strive to conserve the oceans and marine resources and use them sustainably for sustainable development. We hope that children will continue to be able to see the beautiful ocean scenery that we have seen, and that it will remain unchanged.
The facility is equipped with a three-tank activated sludge system. Dyeing wastewater is treated in a raw water pit tank, a pH adjustment tank, and an aeration tank, and the final effluent indicators (BOD, SS, PH) are adjusted to within the standards for discharge into the Sea of Japan.
In addition, a biofilm treatment device is installed between the PH tank and the aeration tank, and specially processed factory wastewater that cannot be treated using the normal activated sludge method is adjusted to meet the discharge standards.
Toyo Saver Co., Ltd. prepares a daily report on the management of the wastewater treatment facility every two weeks. It reports on the transparency of the discharged water and takes appropriate measures.
We have begun observing the following indicator microorganisms using the new equipment.
In order to become a "1001 (Sen'i = Textile) Company" that will continue to exist for 1000 years, we believe that our employees must first be healthy both physically and mentally. We are promoting the health of our employees throughout the company so that each employee can work energetically and maximize their individuality and capabilities.
01
We are working to improve work efficiency to prevent long working hours. We also set recommended days for taking paid leave and collect and manage the rate of leave taken in order to increase the rate of paid leave taken.
02
We implement regular health checkups for 100% of our employees, and after the checkups, we provide appropriate health guidance and recommend secondary checkups. We also subsidize the cost of influenza vaccinations to prevent infectious diseases.
03
With the exception of designated smoking areas, smoking is prohibited anywhere on the premises. We are also currently discussing the possibility of abolishing smoking areas.